What You Need to Know About Industrial Rubber Manufacturing
Discover the essential insights into industrial rubber manufacturing—from custom molding to high-performance bridge bearing pads—with a narrative that ties every detail together for modern infrastructure and aerospace projects.
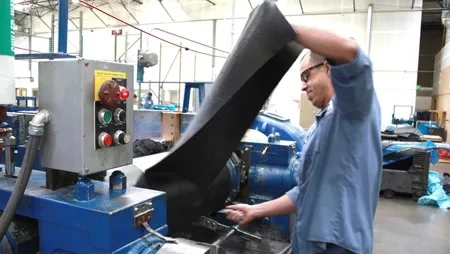
Imagine a world where every bridge, aircraft, and critical piece of infrastructure is supported by materials engineered with precision and passion. Industrial rubber manufacturing is the quiet force that transforms raw materials into the vital components our modern society relies on. In this article, we take you on a journey through the evolution, innovation, and meticulous craftsmanship behind these essential rubber parts—revealing how each stage connects to ensure safety, durability, and excellence.
The Evolution of Industrial Rubber Manufacturing#
The story of industrial rubber manufacturing is one of constant evolution—a narrative that mirrors the progress of modern engineering. Over the years, what began as rudimentary techniques has blossomed into an advanced science marked by custom engineering, precision testing, and unwavering quality standards. This evolution is more than a historical footnote; it is the backbone of today’s infrastructure and aerospace achievements.
As industries demand materials that can withstand extreme conditions, the transformation in rubber manufacturing processes has become integral to building structures that endure. This progress sets the stage for the next chapters in our story, where specialized components like bridge bearing pads and custom-molded parts take center stage.
Bridging the Gap: Natural vs. Neoprene Bridge Bearing Pads#
No journey is complete without understanding the tools that shape it. In the realm of bridge construction, bearing pads are the unsung heroes that absorb shock and distribute loads evenly. Here, the narrative branches into two distinct yet complementary paths:
- Bridge Bearing Natural Rubber Pads:
These pads are prized for their natural elasticity and resilience. Like a seasoned traveler who adapts to every twist of fate, natural rubber pads excel at absorbing dynamic loads and enduring seismic events—making them a reliable choice for long-term performance.
- Bridge Bearing Neoprene Rubber Pads:
In contrast, neoprene pads stand out with their resistance to weathering, oil, and chemicals. They are the stalwart protectors in harsh environments, ensuring that even when the elements are at their fiercest, the bridge remains stable and secure.
By understanding the strengths of each, engineers can select the optimal solution that fits the unique demands of every project. The interplay between these materials exemplifies how nuanced choices in manufacturing directly impact the overall integrity of critical structures.
Custom Rubber Molding: Crafting Solutions for Government and Industrial Projects#
Building on the foundation of advanced materials, custom rubber molding emerges as the artisan of the industrial world. In a narrative where one size does not fit all, custom molding allows for tailored solutions that precisely meet the rigorous demands of government projects and industrial applications.
Every custom-molded component—whether it be a gasket, a bearing, or a specialized seal—is a testament to craftsmanship. It is here that raw innovation meets meticulous engineering:
- Precision: Each piece is crafted to exact specifications, ensuring a perfect fit and flawless performance.
- Reliability: Rigorous testing and quality control, underscored by certifications like AS9100 and ISO 9001, ensure that every component delivers under pressure.
- Compliance: Adherence to international standards means that these parts are not only effective but also safe, meeting or exceeding regulatory requirements.
This tailored approach underscores a broader narrative: every innovation and meticulous detail in rubber manufacturing is interconnected, culminating in products that power some of our most critical infrastructures.
Quality Certifications: The Backbone of Trust and Performance#
At the heart of this manufacturing narrative lies the unwavering commitment to quality. Certifications such as AS9100 and ISO 9001 are not mere labels—they are integral chapters in the story of trust and reliability. They guarantee that every component, from the smallest O‑Ring to the most robust elastomeric pad, is produced under strict guidelines and tested to withstand the challenges of modern engineering.
These certifications do more than reassure; they empower engineers, construction managers, and government agencies to make informed decisions. In our story, quality certifications serve as the guiding principles that ensure each innovation is not only groundbreaking but also dependable.
The Core Components: Connecting the Dots#
No epic is complete without its cast of characters. In industrial rubber manufacturing, components like O‑Rings, elastomeric pads, and structural bearings play starring roles:
-
O‑Rings:
Essential for sealing and preventing leaks, these small components are the guardians of hydraulic systems and aerospace engineering, ensuring every system operates smoothly. -
Elastomeric Pads:
These pads absorb shock and mitigate vibrations, much like a reliable bridge that withstands the test of time, maintaining stability and protecting structural integrity. -
Structural Bearings:
Critical for supporting heavy loads and enabling controlled movement, these bearings distribute stress evenly, ensuring that the whole structure performs harmoniously.
Each component is a link in a well-established chain, illustrating how every detail in the manufacturing process interlocks to form a cohesive, robust system.
Why This Journey Matters#
Understanding the interconnected world of industrial rubber manufacturing is essential for professionals across various fields. It is not just about choosing a material—it is about comprehending a holistic process where every decision, every test, and every certification plays a pivotal role in building safe and durable infrastructures.
For bridge bearing manufacturers, transportation agencies, and government project managers, this knowledge empowers you to:
- Enhance Project Success: By making informed choices, you mitigate risks and ensure long-lasting performance.
- Optimize Material Selection: Whether choosing natural rubber or neoprene pads, understanding their unique benefits leads to smarter decisions.
- Ensure Compliance and Safety: With quality certifications as your benchmark, you can confidently meet the stringent demands of modern construction and aerospace projects.
Key Takeaways#
- Innovation in industrial rubber manufacturing has evolved into a precise science essential for modern infrastructure and aerospace projects.
- Bridge bearing pads come in natural rubber and neoprene variants, each offering unique advantages depending on environmental demands.
- Custom rubber molding provides bespoke solutions that meet the exacting standards of government and industrial applications.
- Quality certifications like AS9100 and ISO 9001 are the cornerstones of reliability and performance.
- Key components such as O‑Rings, elastomeric pads, and structural bearings work together to ensure the longevity and safety of critical systems.
Conclusion and Call to Action#
The narrative of industrial rubber manufacturing is one of innovation, precision, and an unyielding commitment to quality. Each chapter—from the evolution of manufacturing techniques to the intricate details of custom molding and quality certifications—interconnects to build the robust infrastructure that underpins our modern world.
If you’re ready to explore how these finely engineered rubber solutions can elevate your next project, learn more about our products and services. Discover how a deep understanding of every link in this manufacturing chain can lead to safer, more durable, and more innovative infrastructures.